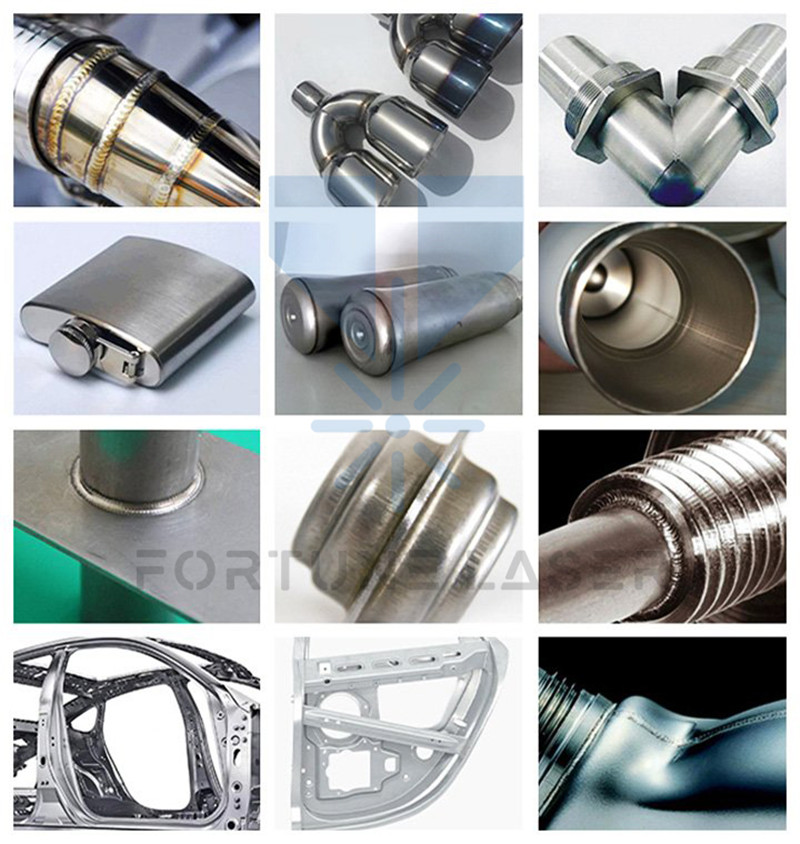
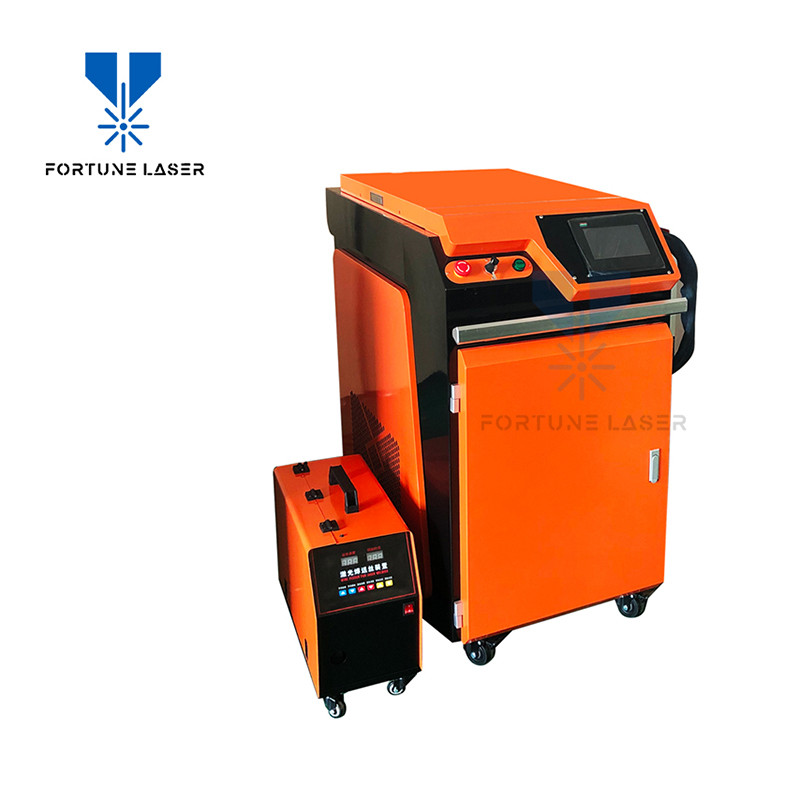
Fortune Laser Handheld Fiber Laser Welding Machine
The handheld fiber laser welding machine, also called Portable Handheld Laser Welder, is a new generation of laser welding equipment, which belongs to non-contact welding. The operation process does not require pressure. The working principle is to directly irradiate a high-energy intensity laser beam on the surface of the material through the interaction of the laser and the material. The material is melted inside, and then cooled and crystallized to form a weld.

Continuous Laser Welding Machine
The Fortune Laser continuous optical fiber CW laser welding machine is consist of welding body, welding working table, water chiller and controller system etc. This series of equipment is 3-5 times of the speed than the traditional optical fiber transmission laser welding machine. It can precisely weld flat, circumference, line type products and non-standard customized production lines.

Jewelry Mini Spot Laser Welder 60W 100W
This 60W 100W YAG mini spot laser welder, also knew as portable jewelry laser soldering machine, is specially developed for laser welding of jewelry, and mainly used in perforating and spot welding of gold and silver jewelry. The laser spot welding is an important aspect of laser process technology application.

Robotic Fiber Laser Welding Machine
Fortune Laser robot laser welding machine is composed of a dedicated fiber laser head, a high-precision capacitance tracking system, a fiber laser and an industrial robot system. It is an advanced equipment for flexible welding of metal sheets of different thicknesses from multiple angles and multiple directions.
The combination of laser welding and robots has the advantages of automation, intelligence, and high flexibility, and can be used for welding complex surface materials.